Laser Marking on Aluminum: how It works and why It's crucial in the Automotive Industry
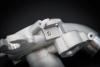
In this article, we’ll explore how laser marking on aluminum works, how to achieve white and black markings, and why it is essential for industrial traceability through 2D codes like DataMatrix.
What is Laser Marking on Aluminum?
Laser marking on aluminum involves the use of a focused laser beam to modify the surface of the metal to create permanent symbols, codes, text, or logos.
The most common lasers used for marking aluminum are:
- Fiber lasers – highly efficient, ideal for high-contrast markings.
- CO₂ lasers – less commonly used on bare metal but suitable for treated surfaces.
- MOPA lasers – especially suited for color marking on metals, including white and black tones.
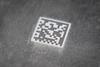
How is the Color White Achieved in Laser Marking on Aluminum?
One of the most sought-after results in aluminum laser marking is the white color, ideal for creating high-contrast codes on dark or anodized surfaces.
White at the Molecular Level
White marking is not the result of added material, but rather an optical effect derived from the microstructure of the surface modified by the laser.
- The laser, through extremely short pulses (often with MOPA lasers), heats the surface in a controlled way without melting the material.
- This causes micro-crystallization or a surface refinement that diffuses light uniformly, creating a bright white visual effect.
- There is no significant oxidation: the color results from optical interference and diffuse reflection.
White is highly valued because it can be read even by optical systems, making it useful in automated traceability processes.
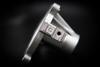
How is the Color Black Achieved on Aluminum Surfaces?
Unlike white, black coloring in laser marking on aluminum results from controlled oxidation or more intense thermal modifications.
Black at the Molecular Level
- The laser induces deeper localized heating, triggering oxidation reactions (formation of dark aluminum oxide).
- It may also alter the surface roughness, which reduces light reflection.
- The result is a surface with higher optical absorption, perceived as black.
Black is extremely useful for permanent, high-contrast markings, ideal in industrial environments exposed to wear, chemicals, or heat.
Watch the Video on Youtube
Laser Marking on Aluminum in the Automotive Industry
The automotive sector uses aluminum in many of its components, especially die-cast parts (such as engine mounts, brackets, housings, etc.), due to the material’s light weight and strength.
Why laser marking is crucial:
- Traceability: each component must be identifiable with unique codes (e.g., DataMatrix or QR codes).
- Durability: the marking must withstand mechanical stress, oils, solvents, and high temperatures.
- Precision: the quality of the laser beam allows marking even on curved or irregular surfaces.
- Automation: the process is easily integrated into production lines.
A laser-marked 2D code can contain information about:
- Part origin
- Production batch
- Technical specifications
- Any revisions
This enables complete traceability throughout the entire production and post-sale supply chain, improving recall management and overall product quality.
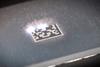
The Importance of This Process
Laser marking on aluminum is not just an aesthetic feature but a key element for efficiency and reliability in industrial settings, particularly in the automotive sector.
The ability to obtain white and black markings through precise physico-chemical processes provides permanent, readable and resistant identification.
With the integration of 2D codes like DataMatrix, laser marking becomes a pillar of smart manufacturing and Industry 4.0 traceability.